6 Axis Industrial Robot Arm Szgh-I5 Collaborative Robot 6 Axis Industrial Robot Arm 5kg Payload
6 Axis Industrial Robot Arm Szgh-I5 Collaborative Robot 6 Axis Industrial Robot Arm 5kg Payload
Main Category
Industrial robot arm /Collaborative robot arm / Electric gripper/Intelligent actuator/Automation solutions
Application
The TM5-700 is our most compact cobot that can be easily integrated into any production line. Designed with a built-in vision system specifically for flexible production needs required by small parts assembly, and production processes in consumer electronics and consumer goods. Our robot offers great versatility for small to medium-sized businesses. TM5-700’s size is also quick to deploy and easy to fit into existing factory environments.
With a class-leading vision system, advanced AI technology, comprehensive safety, and easy operation, AI Cobot will take your business further than ever. Take automation to the next level by boosting productivity, improving quality, and reducing costs.
Introducing an advanced and versatile 6-axis robotic arm with an exceptional 5kg payload capacity, this collaborative robotic arm is a game changer in robotics. With its collaborative design, it can easily adapt and work alongside human operators, making it a truly great tool for a variety of industries.
The 6-axis robotic arm is designed to increase productivity and efficiency in the manufacturing process. Its six-axis design provides the arm with a wide range of motion, enabling it to perform complex tasks with high precision. Whether assembling small electronic components or handling heavy mechanical parts, this robotic arm provides exceptional performance in any situation.
With a maximum payload capacity of 6 kg, the robotic arm is capable of handling a variety of objects. This makes it ideal for industries dealing with varying product sizes and weights. It is able to handle heavier items without manual lifting and reduces the risk of workplace injuries. With this collaborative robot arm, businesses can increase productivity while maintaining a safe and efficient work environment.
What makes this cobot arm unique is its ability to collaborate. It is equipped with advanced sensors and safety features that can detect the presence of humans and automatically adjust its movements to ensure the safety of those around it. This feature allows human operators to work side-by-side with the robotic arm, maximizing productivity through efficient collaboration.
The 6-axis robot arm is designed with user-friendliness in mind. It is easily programmed and controlled through intuitive software, making it easy to use for both experienced technicians and beginners. This ease of use ensures smooth integration into existing production lines, minimizing downtime and maximizing productivity.
In summary, a 6-axis robotic arm with a 5kg payload capacity, collaborative design, and collaborative capabilities is an excellent choice for businesses looking to enhance their manufacturing processes. Its versatility, precision and safety make it an invaluable tool in a variety of industries. Increase productivity, improve workplace safety and simplify your operations with this superior robotic arm.
Features
SMART
Future-proof Your Cobot with AI
• Automated optical inspection (AOI)
• Quality assurance & consistency
• Increase production efficiency
• Reduce operating costs
SIMPLE
No experience required
• Graphical interface for easy programming
• Process-oriented editing workflow
• Simple hand guiding for positions teaching
• Fast visual calibration with calibration board
SAFE
Collaborative safety is our priority
• Complies with ISO 10218-1:2011 & ISO/TS 15066:2016
• Collison detection with emergency stop
• Save the cost and space for barriers & fencing
• Set up speed limits in a collaborative workspace
AI-powered cobots recognize the presence and orientation of their environment and parts to perform visual inspections and dynamic pick-and-place tasks. Effortlessly apply AI to the production line and increase productivity, decrease costs, and shorten cycle times. AI vision can also read results from machines or test equipment and make appropriate decisions accordingly.
Besides improving automation processes, an AI-driven cobot can track, analyze, and integrate data during production to prevent defects and improve product quality. Easily enhance your factory automation with a complete set of AI technology.
Our collaborative robots are equipped with an integrated vision system, giving cobots the ability to perceive their surroundings which significantly enhances cobot capabilities. Robot vision or the ability to “see” and interpret visual data into command prompts is one of the features that makes us superior. It is a game-changer for accurately performing tasks in dynamic changing workspaces, making operations run smoother, and automation processes more efficiently.
Designed with first-time users in mind, programming knowledge is not a prerequisite to get started with AI Cobot. An intuitive click-and-drag motion using our flow programming software reduces the complexity. Our patented technology allows operators with no coding experience to program a project as short as five minutes.
Inherent safety sensors will stop AI Cobot when physical contact is detected, minimizing the potential damage for a pressure-free and safe environment. You can also set up speed limits for the robot so it can be used in a variety of environments right next to your workers.
Related Products
Specification Parameter
Model |
TM5M-700 |
|
Weight |
22.1KG |
|
Maximum Payload |
6KG |
|
Reach |
700mm |
|
Joint Ranges |
J1,J6 |
±270° |
J2,J4,J5 |
±180° |
|
J3 | ±155° | |
Speed |
J1, J2, J3 |
180°/s |
J4, J5, J6 |
225°/s |
|
Typical Speed |
1.1m/s |
|
Max. Speed |
4m/s |
|
Repeatability |
± 0.05mm |
|
Degree of freedom |
6 rotation joints |
|
I/O |
Control box |
Digital input:16 Digital output:16 Analog input:2 Analog output:1 |
Tool Conn. |
Digital input:4 Digital output:4 Analog input:1 Analog output:0 |
|
I/O Power Supply |
24V 2.0A for control box and 24V 1.5A for tool |
|
IP Classification |
IP54(Robot Arm); IP32(Control Box) |
|
Power Consumption |
Typical 220 watts |
|
Temperature |
The robot can work in a temperature range of 0-50℃ |
|
Cleanliness |
ISO Class 3 |
|
Power Supply |
22-60 VDC |
|
I/O Interface |
3xCOM, 1xHDMI, 3xLAN, 4xUSB2.0, 2xUSB3.0 |
|
Communication |
RS232, Ethemet, Modbus TCP/RTU (master & slave), PROFINET (Optional), EtherNet/IP(Optional) |
|
Programming Environment |
TMflow, flowchart based |
|
Certification |
CE, SEMI S2 (Option) |
|
AI & Vision*(1) |
||
AI Function |
Classification, Object Detection, Segmentation, Anomaly Detection, AI OCR |
|
Application |
Positioning, 1D/2D Barcode Reading, OCR, Defect Detection, Measurement, Assembly Check |
|
Positioning Accuracy |
2D Positioning: 0.1mm*(2) |
|
Eye in Hand (Built in) |
Auto-focused color carmera with 5M resolution, Working distance 100mm ~ ∞ |
|
Eye to Hand (Optional) |
Support Maximum 2xGigE 2D cameras or 1xGigE 2D Camera +1x3D Camera*(3) |
|
*(1) No built-in vision robot arms TM5X-700, TM5X-900 are also available.
*(2) The data in this table are measured by TM laboratory and the working distance is 100mm. It should be noted that in practical applications, the relevant values may be different due to factors such as the on-site ambient light source, object characteristics, and vision programming methods that will affect the change in accuracy. *(3)Refer to the official website of TM Plug & Play for camera models compatible to TM Robot. |
Our Business
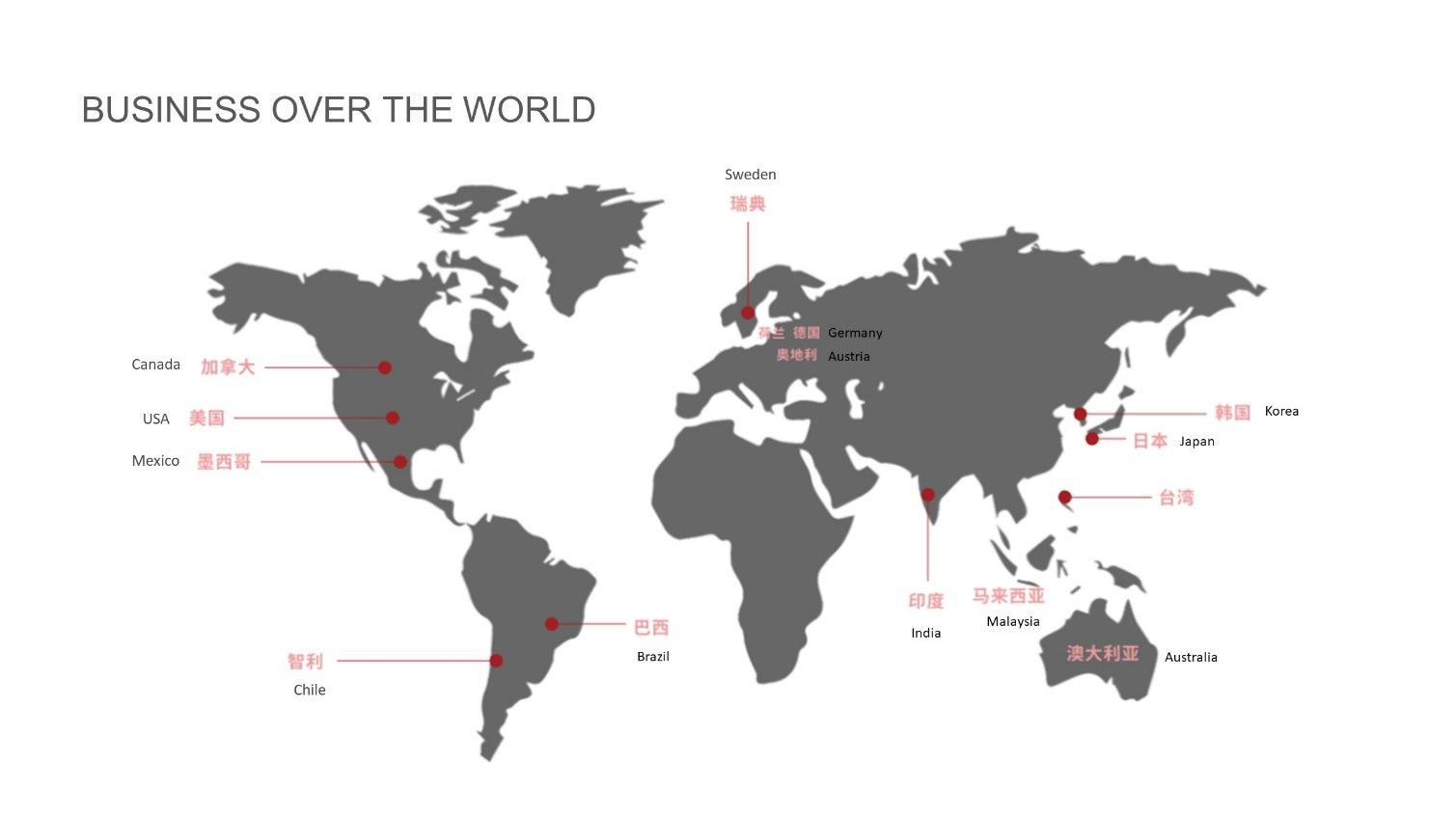
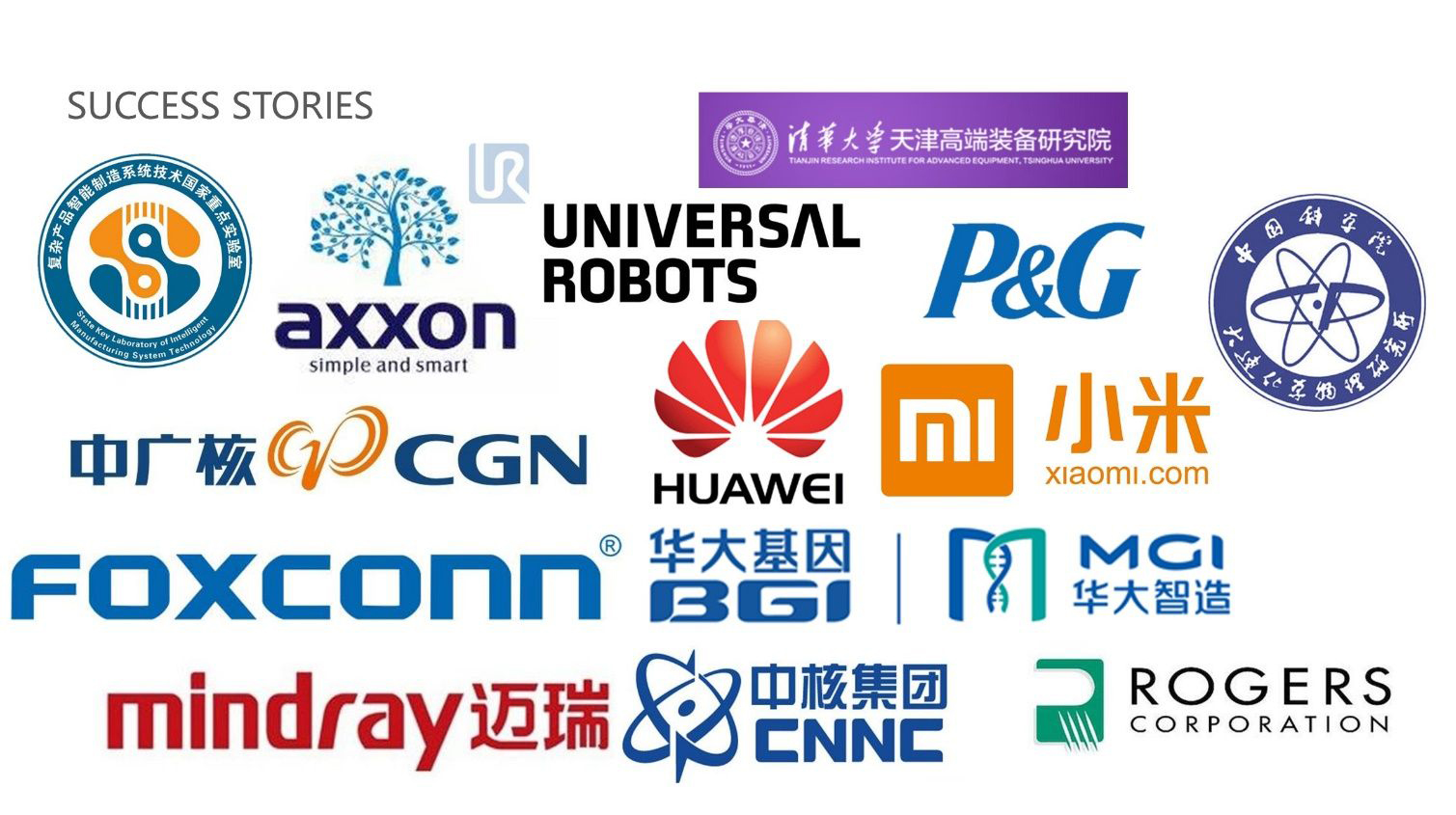