Collaborative Robot Gripper – SFG Soft Finger Gripper Cobot Arm Gripper
Main Category
Industrial robot arm /Collaborative robot arm / Electric gripper/Intelligent actuator/Automation solutions/cobot arm gripper/soft gripper/robot arm gripper
Application
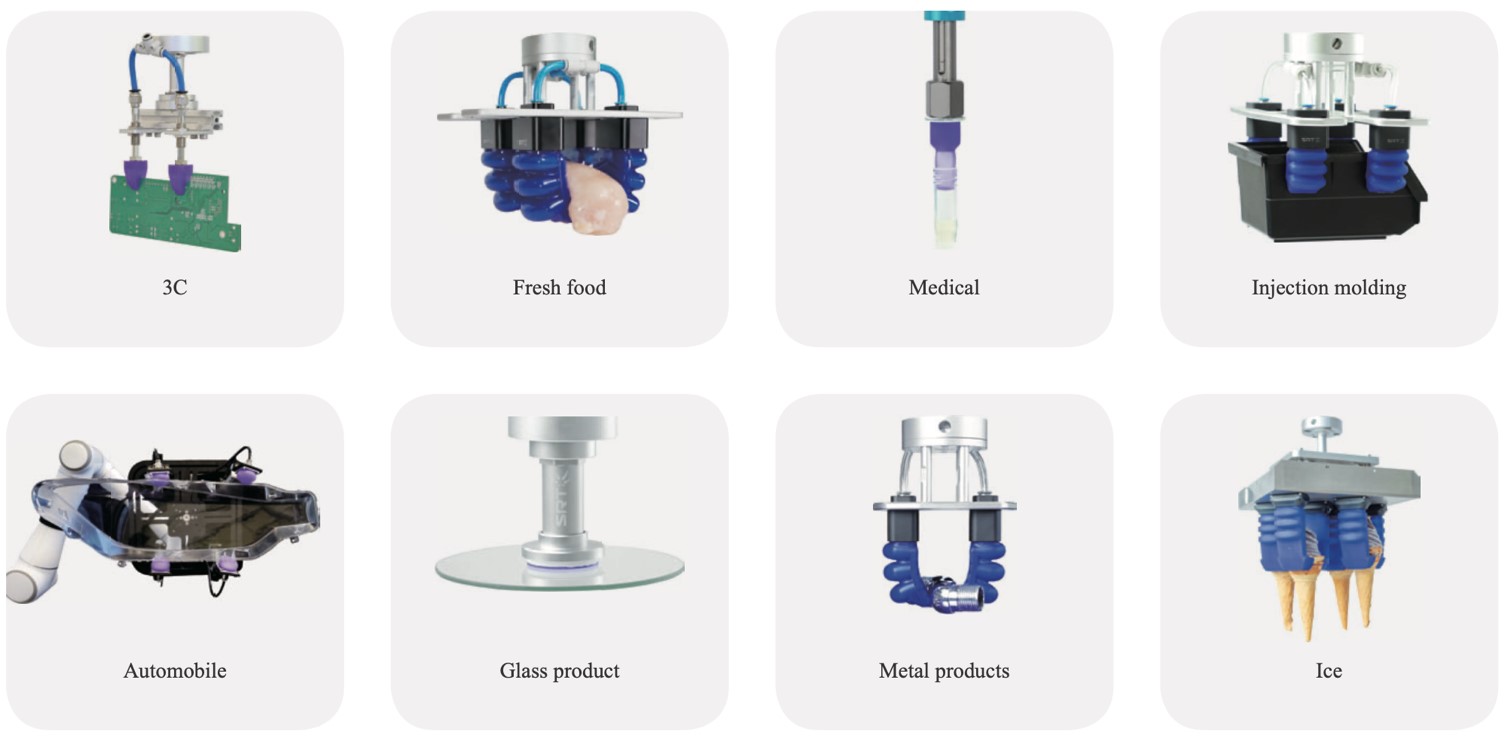
SCIC SFG-Soft Finger Gripper is a new type flexible robotic arm gripper developed by SRT. Its main components are made of flexible materials. It can simulate the grasping action of human hands, and can grasp objects of different sizes, shapes and weights with one set of gripper. Different from the rigid structure of traditional robotic arm gripper, the SFG gripper has soft pneumatic "fingers", which can adaptively wrap the target object without pre-adjustment according to the precise size and shape of the object, and get rid of the restriction that traditional production line requires equal size of the production objects. The finger of the gripper is made of flexible material with gentle grasping action, which is especially suitable for grasping easily damaged or soft indeterminate objects.
In the robotic arm gripper industry, the commonly used traditional clamps including cylinder grippers, vacuum chucks, etc. are often affected by factors such as product shape, category, location, etc., and is unable to grip the object smoothly. The soft gripper based on flexible robot technology developed by SRT can perfectly solve this industrial problem and make the automatic production line take a qualitative leap.
Feature
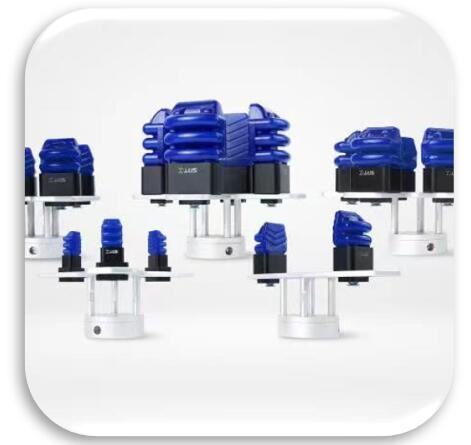
·NO restrictions of object shape, size & weight
·300CPM operating frequency
·repeatability accuracy 0.03mm
·max. payload 7kg
● Soft gripper has special airbag structure, producing different movements according to internal and external pressure difference.
● Input positive pressure: it tends to grip, self-adaptively covering the interface of workpiece, and completing grasping movement.
●Input negative pressure: the grippers open and release the workpiece and completes internal supporting grasping in some specific situations
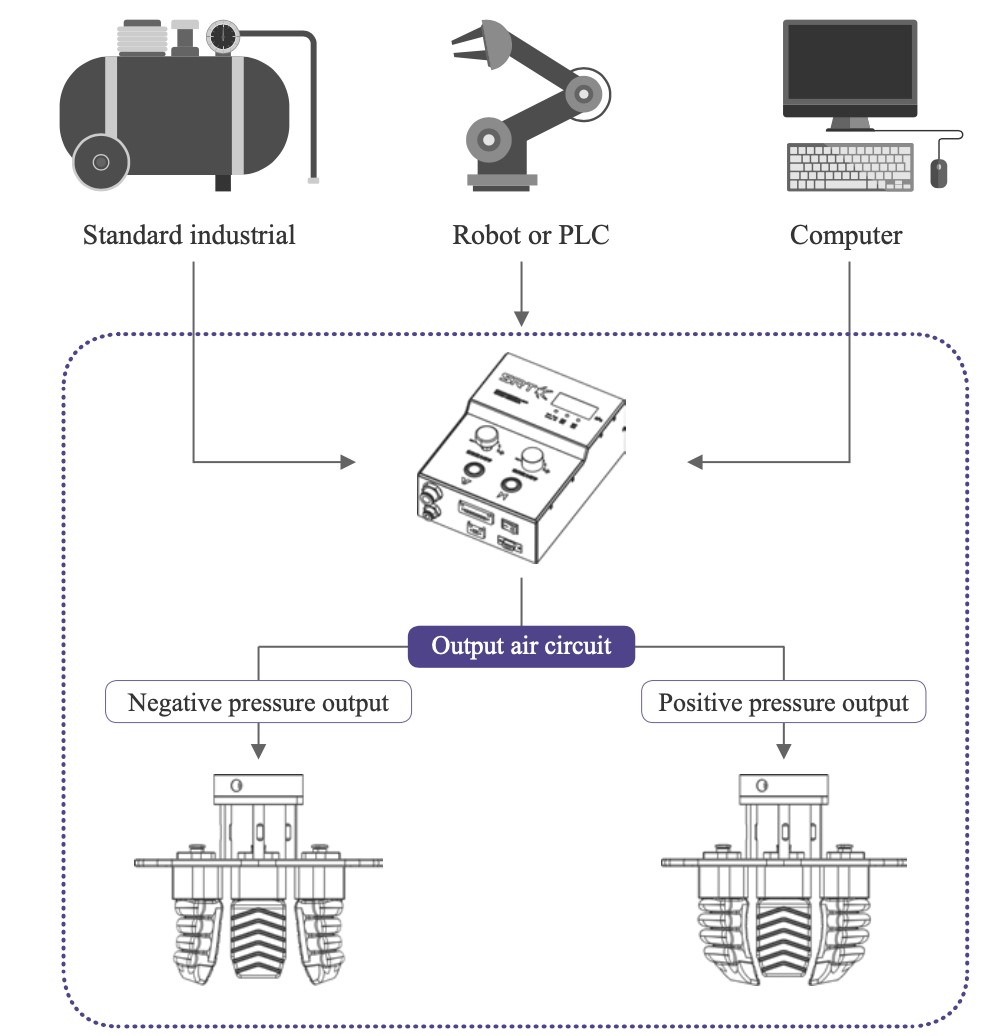
SFG soft grippers have been deployed with world class collaborative robot arms, including:
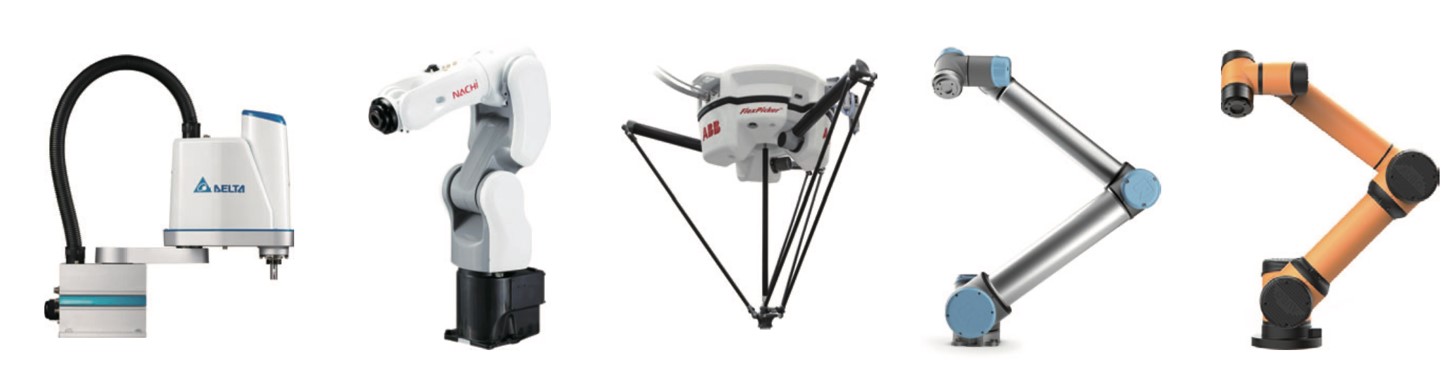
4-axis horizontal (SCARA) robot Delta
Industrial robot arm Nachi Fujikoshi
4-axis parallel (Delta) robot ABB
6-axis collaborative robot UR
6-axis collaborative robot AUBO
Specification Parameter
This soft gripper is suitable for small-scale automatic devices in industries such as intelligent assembly, automatic sorting, logistics warehouse and food processing, and also could be applied as a functional part in scientific research laboratory, intelligent entertainment equipment and serving robots. It is an ideal choice for guests who need intelligent, damage-free, highly safe and highly adaptable grasping motions.
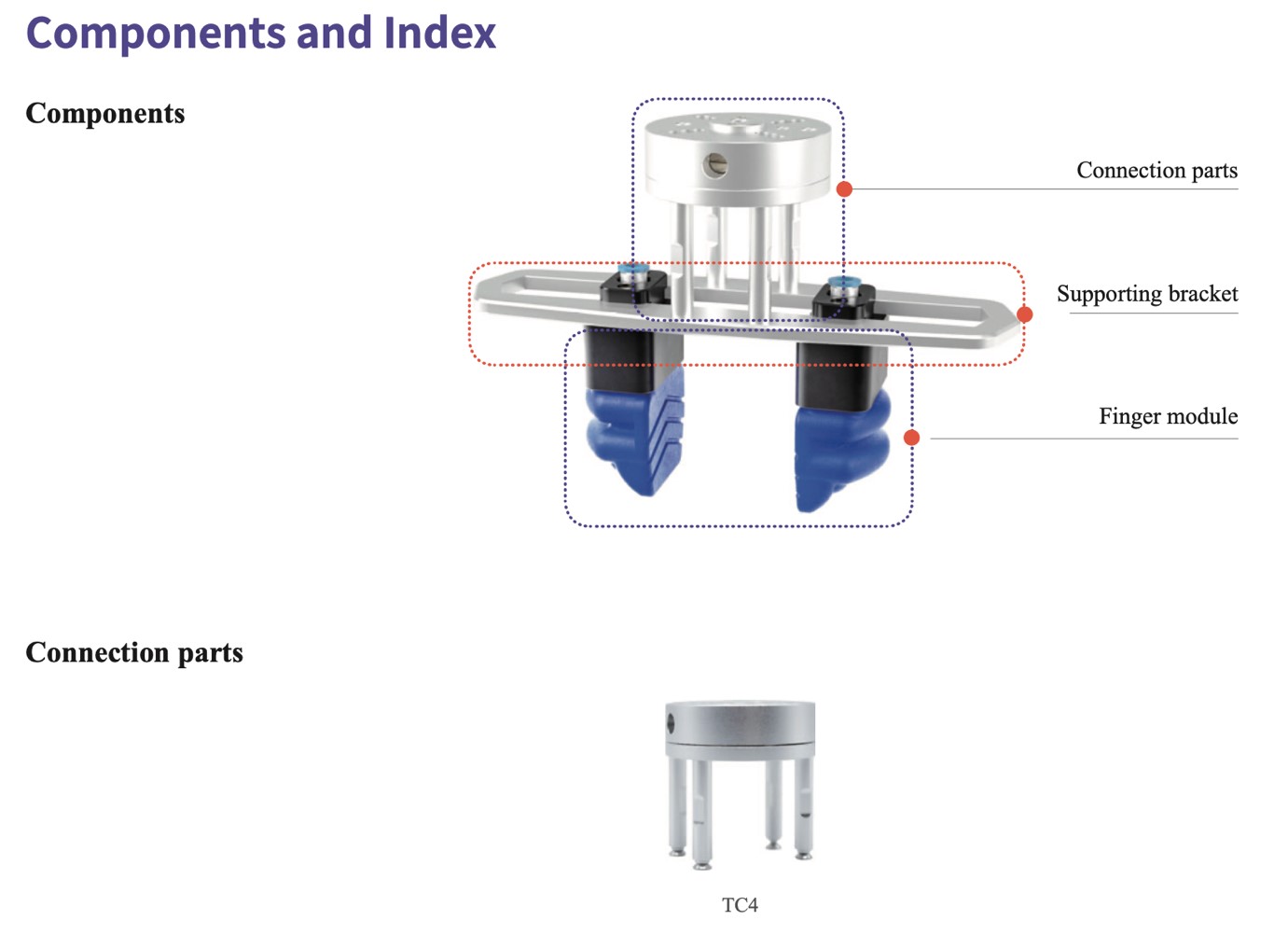
SUPPORTING BRACKETS:

FINGER MODULES:
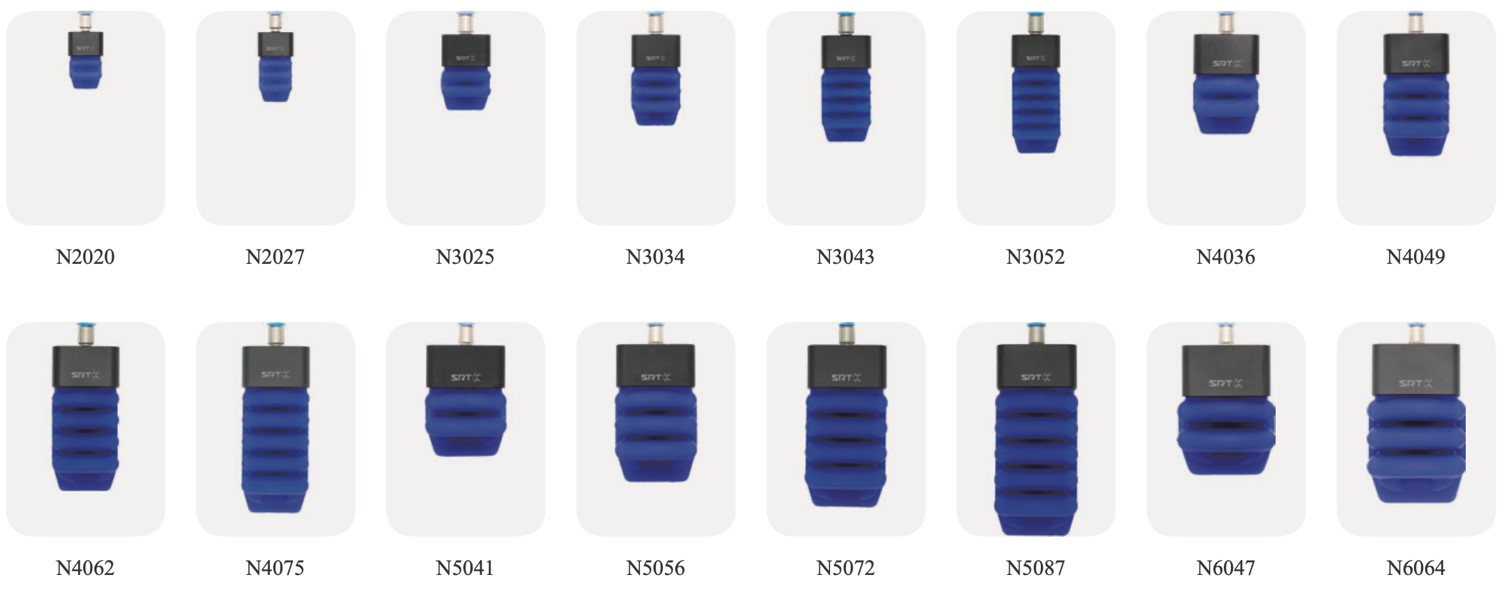
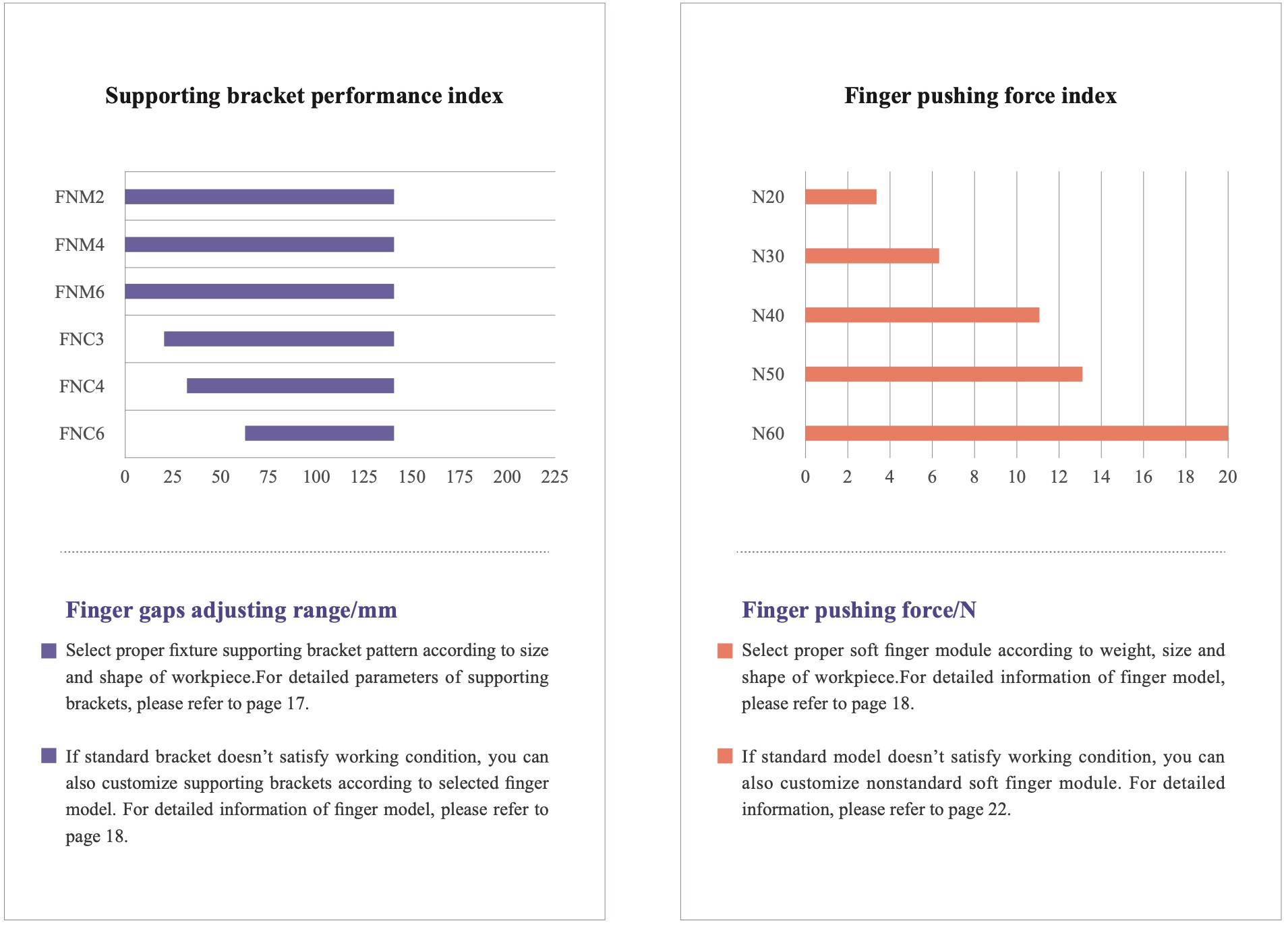
CODING PRINCIPLES
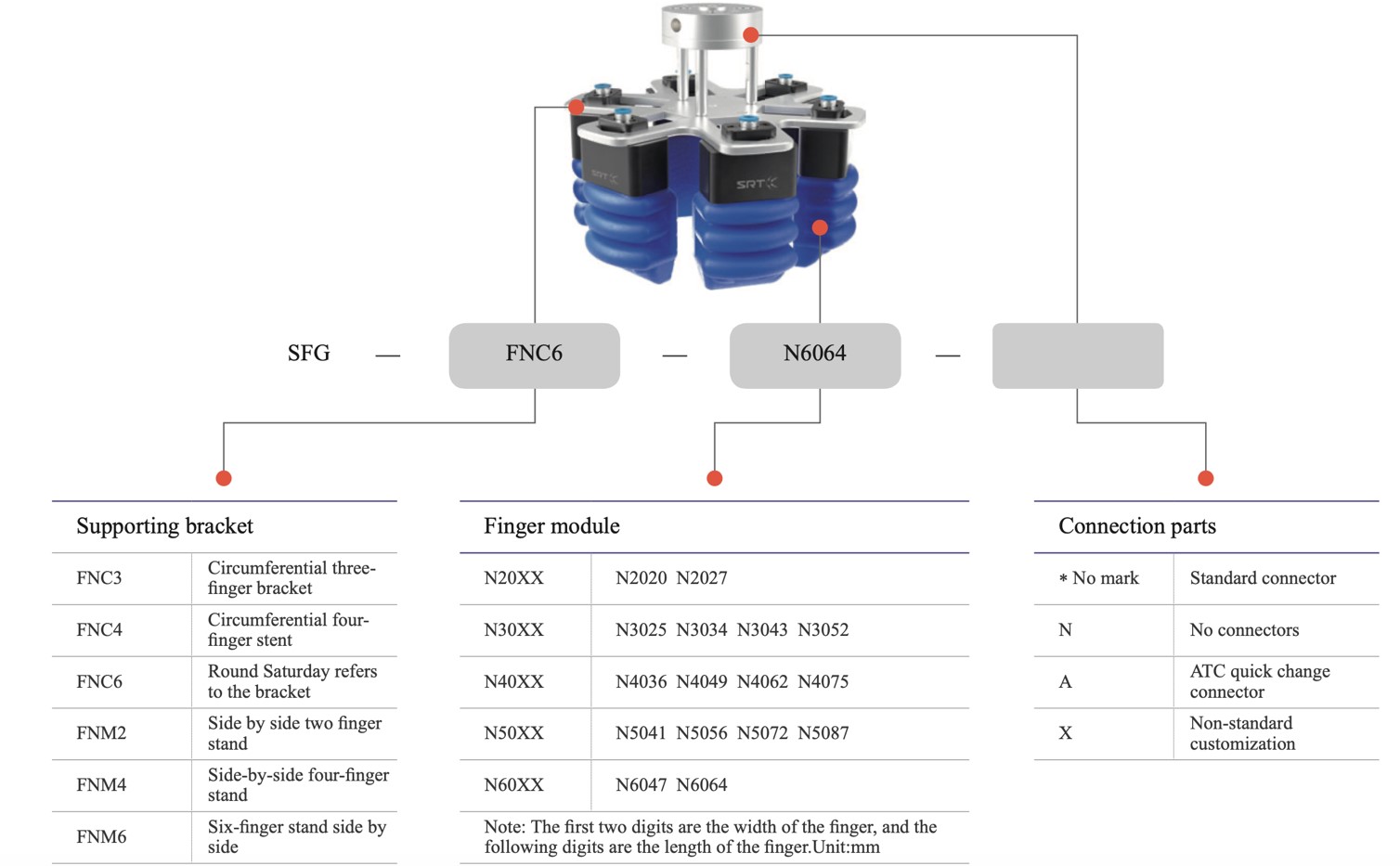
FINGURES CODING PRINCIPLES
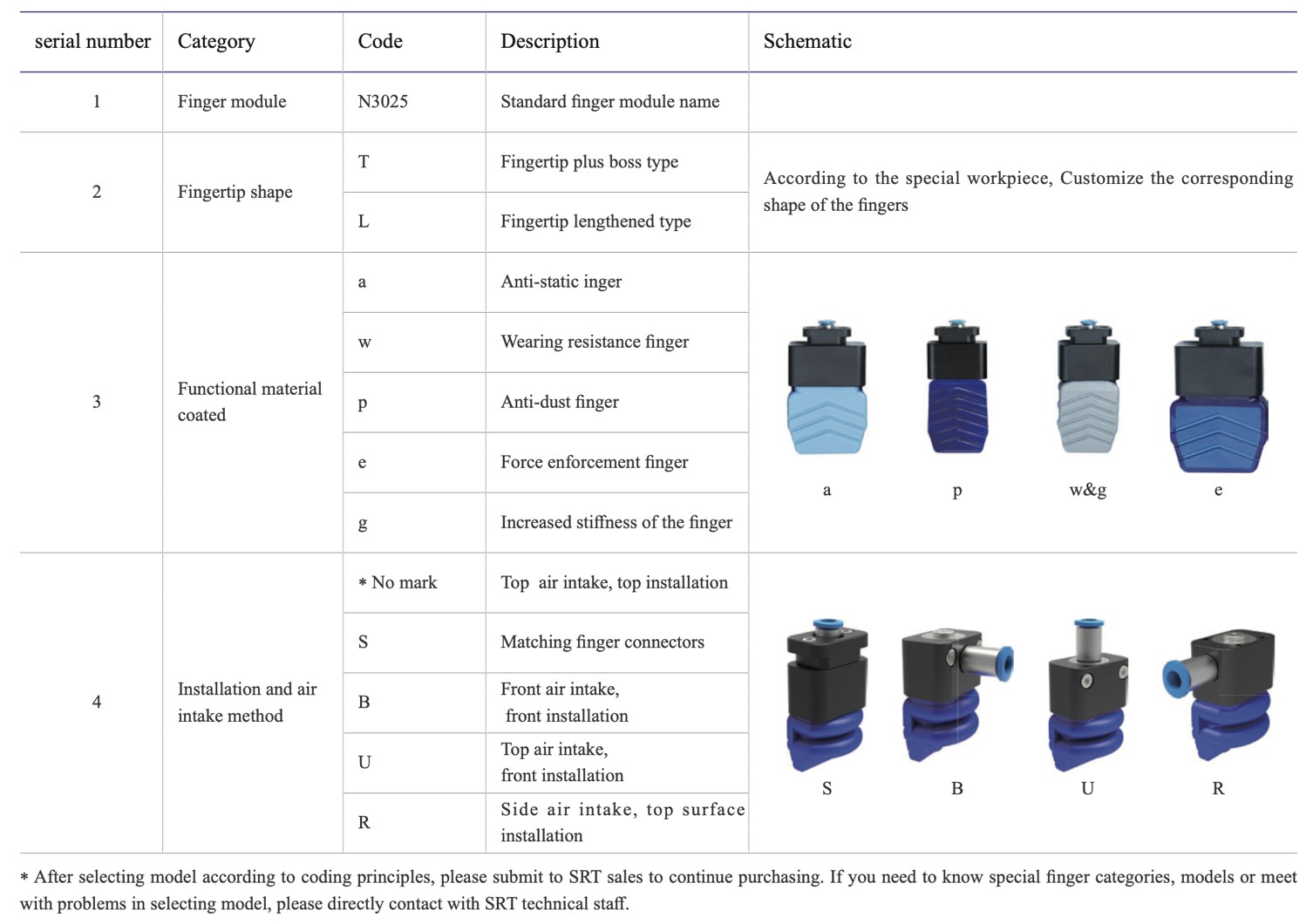
Mounting part
Connection parts
TC4 is a modular accessory that cooperates with the SFG series of flexible gripper and the mechanical connection of the machine. Fast deployment and rapid replacement of fixtures can be completed by loosening fewer screws.
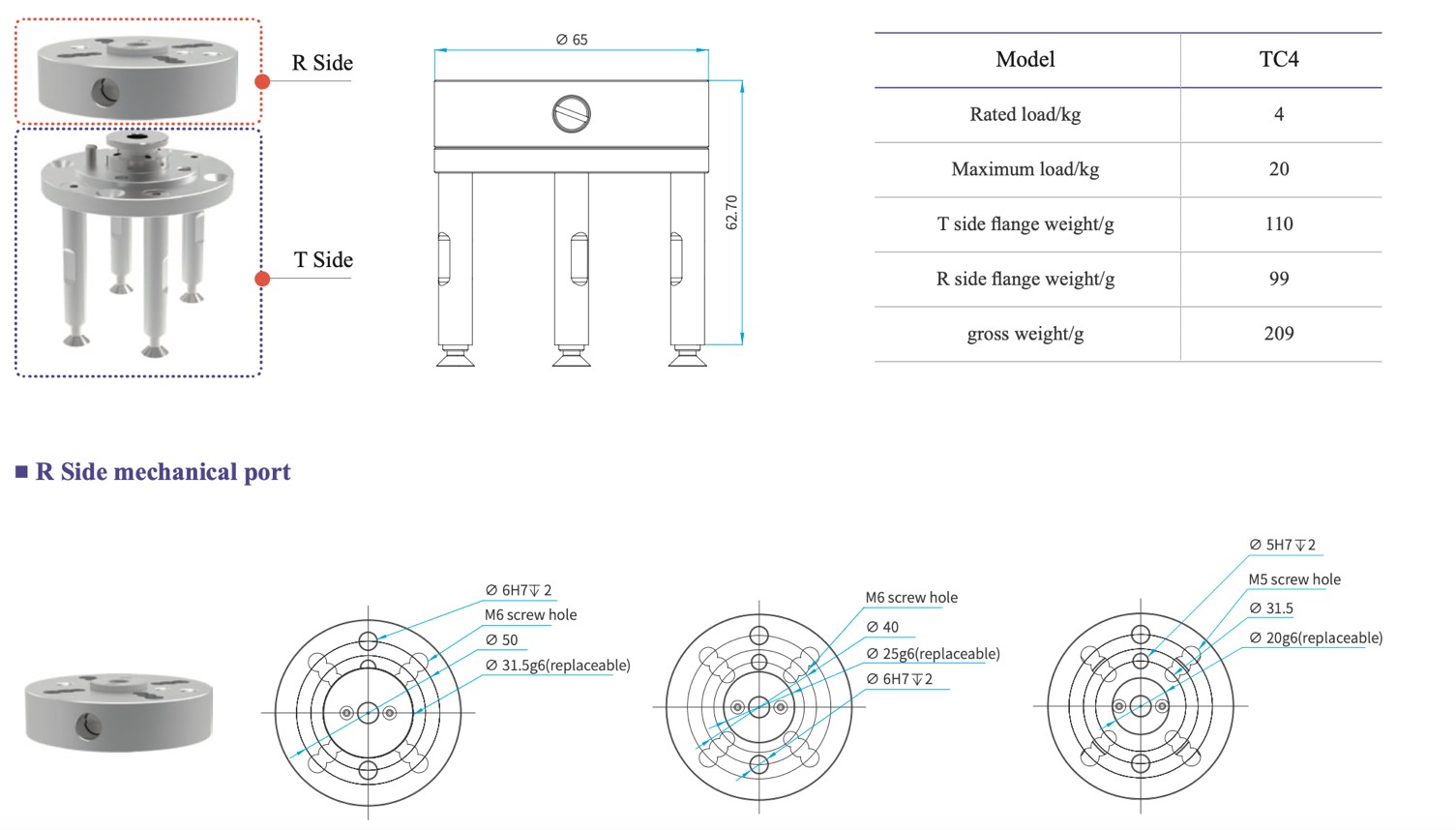
Supporting bracket
■ FNC Circumferential bracket
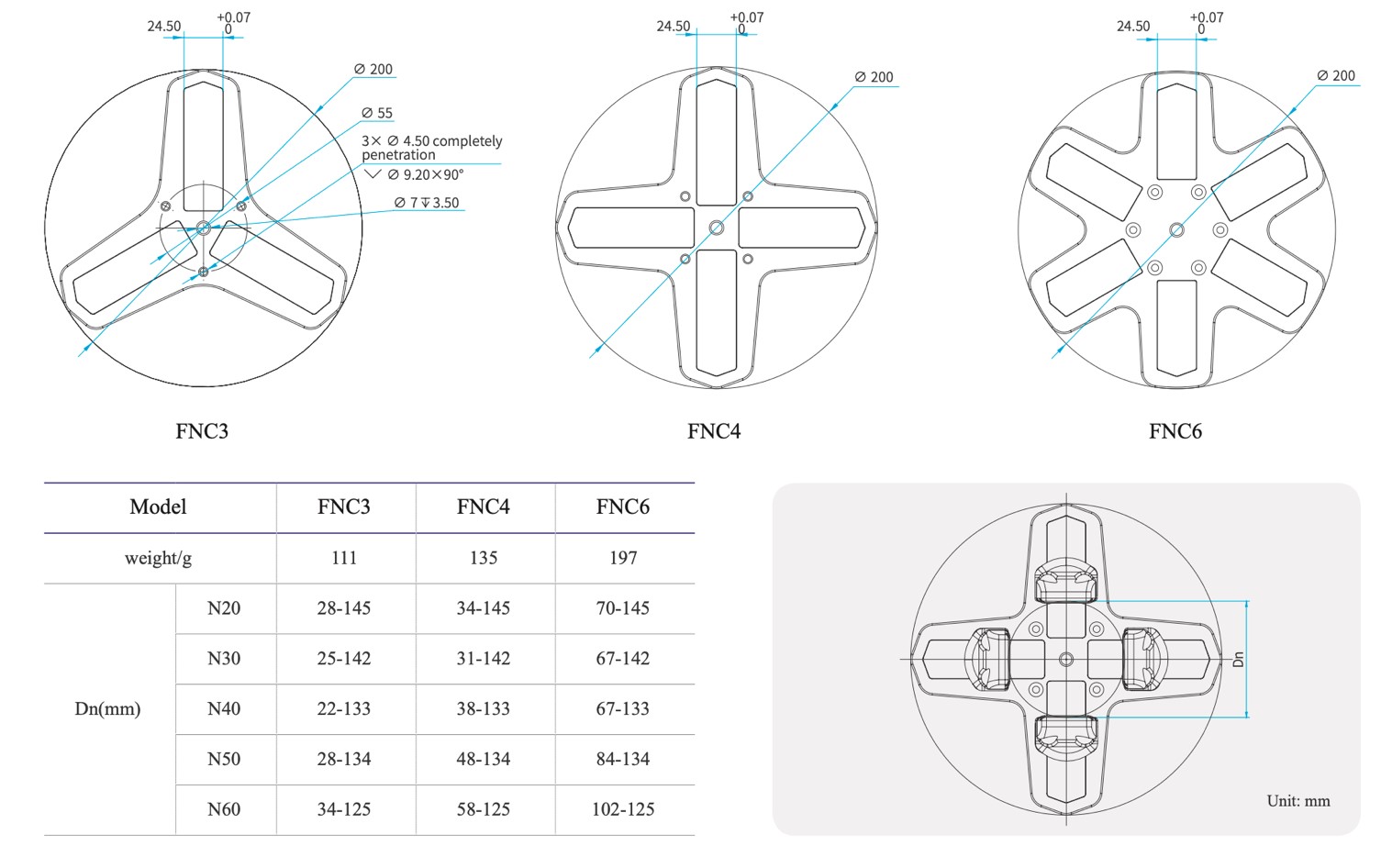
■ FNM Side by side stand
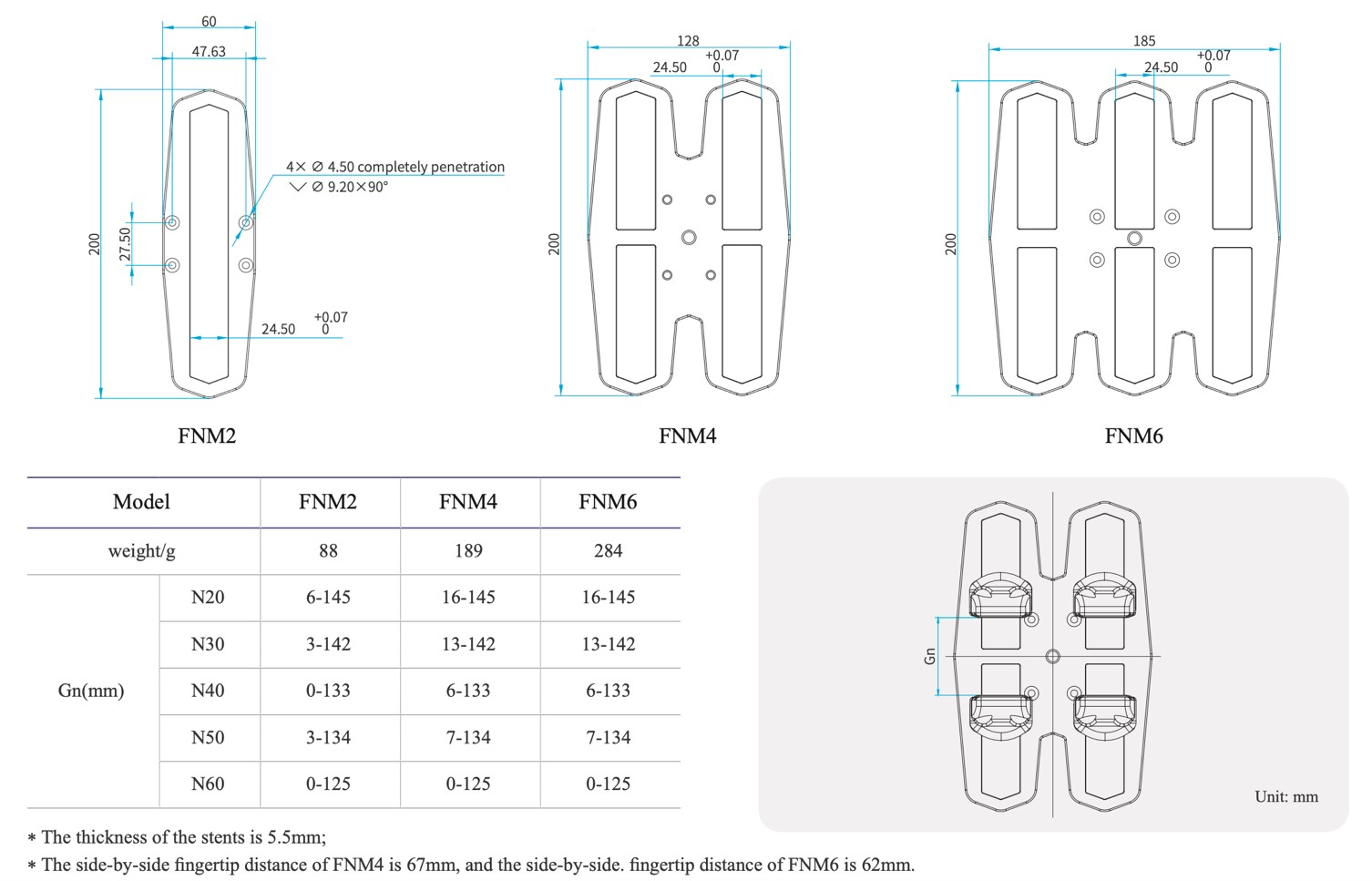
soft finger module
The flexible finger module is the core component of the SFG soft finger gripper. The executive part is made of food-grade silicone rubber, which is safe, reliable and highly flexible. The N20 series are suitable for picking small items; N40/N50 fingers have a rich variety of fingers, a wide range of grasping, and mature technology.
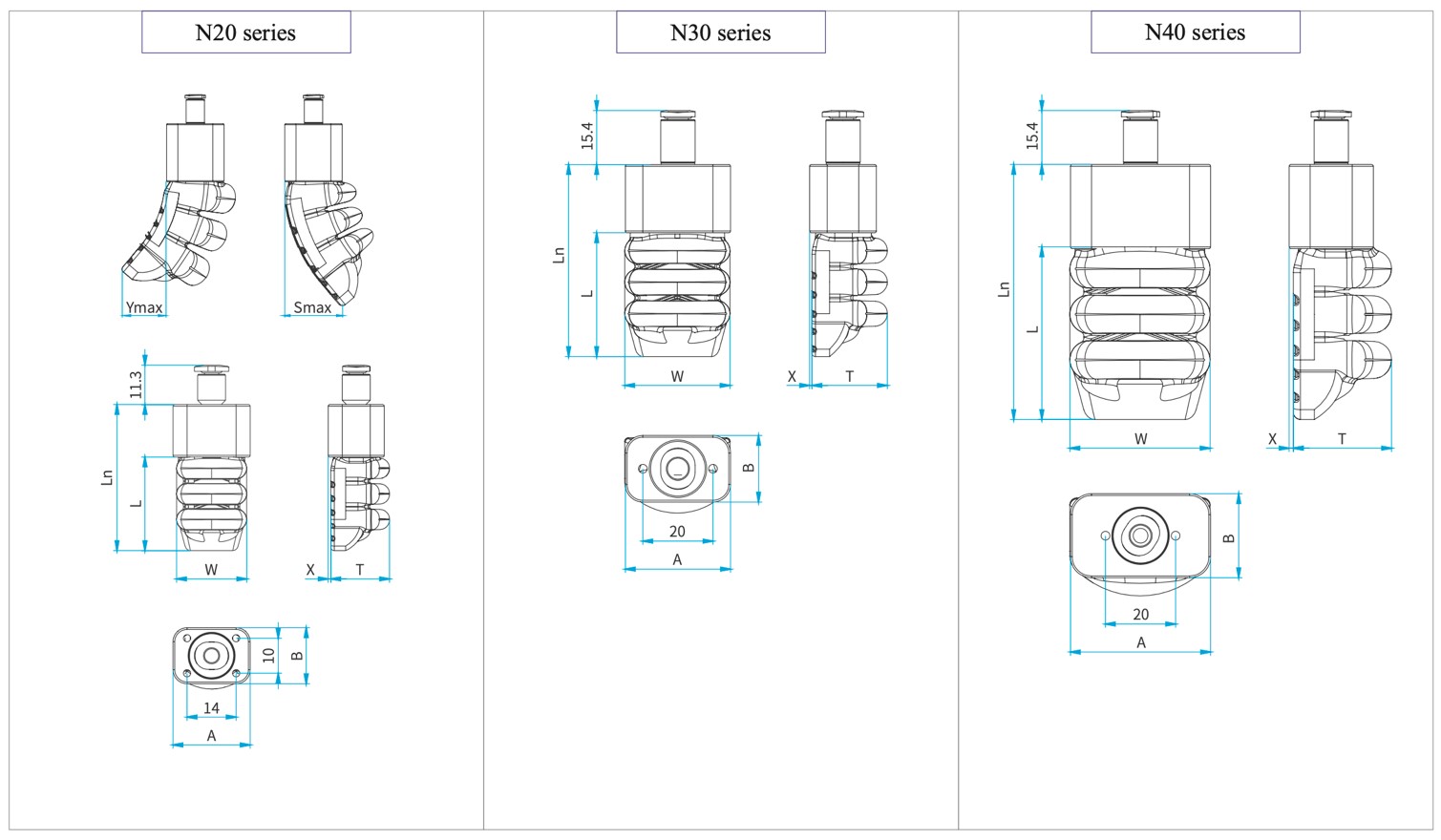
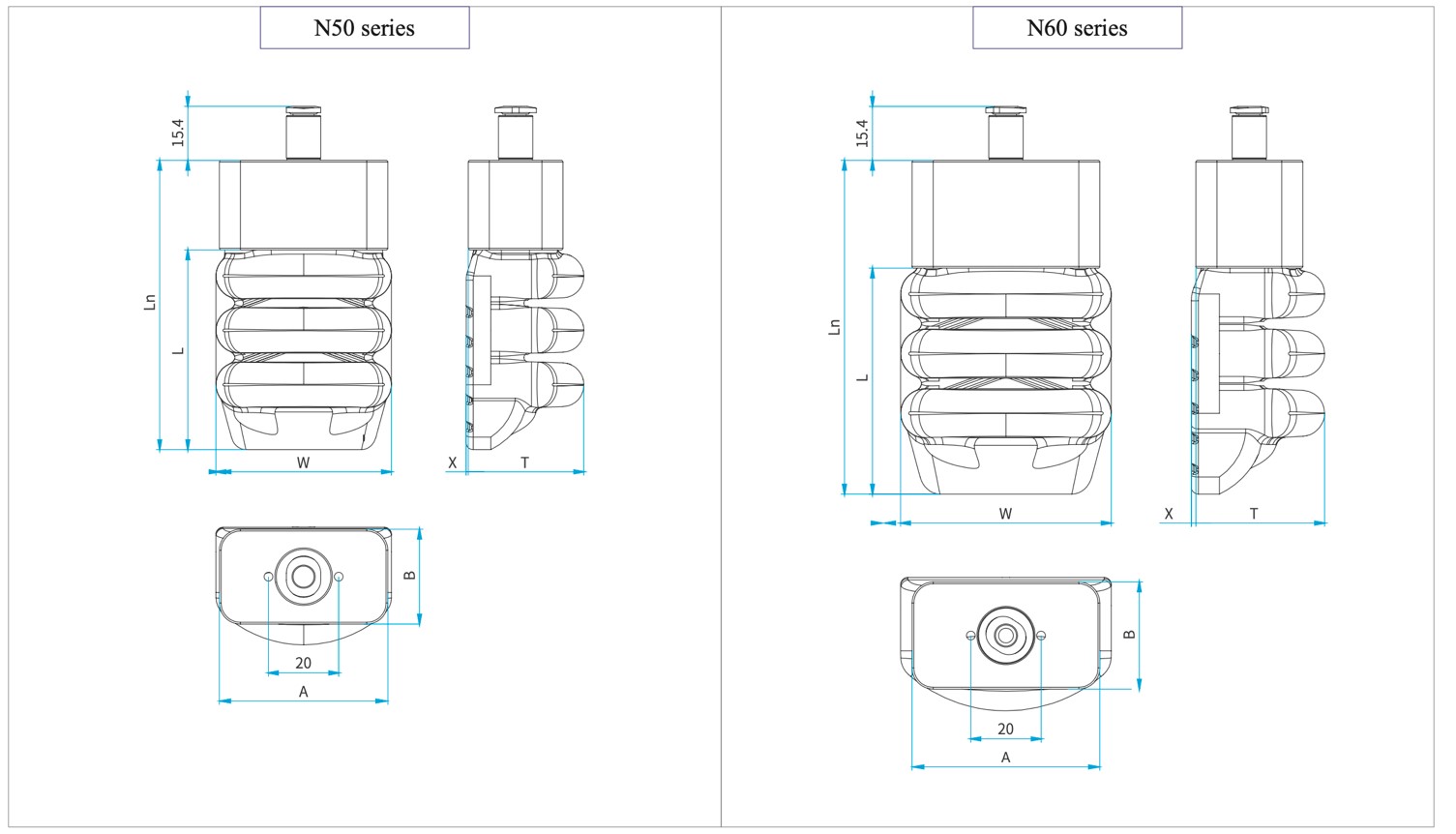
ModelParameter |
N2020 |
N2027 |
N3025 |
N3034 |
N3043 |
N3052 |
N4036 |
N4049 |
N4062 |
N4075 |
N5041 |
N5056 |
N5072 |
N5087 |
N6047 |
N6064 |
|
W/mm |
20 |
30 |
40 |
50 |
60 |
||||||||||||
L/mm |
19.2 |
26.5 |
25 |
34 |
45 |
54 |
35.5 |
48.5 |
62.5 |
75 |
40.5 |
56 |
73 |
88 |
47 |
64 |
|
Ln/mm |
34.2 |
41.5 |
44 |
53.5 |
64 |
73 |
59.5 |
72.5 |
86.5 |
99 |
66 |
81.5 |
98.5 |
113.5 |
77.7 |
94.7 |
|
T/mm |
16 |
16.8 |
20.5 |
21.5 |
22 |
22 |
26.5 |
28 |
28.5 |
28.5 |
31.5 |
33.5 |
33.5 |
34 |
35.2 |
38 |
|
X/mm |
1.5 |
1.5 |
1.5 |
1.5 |
1.5 |
1.5 |
0 |
0 |
-0.5 |
-0.5 |
1.5 |
1.5 |
0 |
0.5 |
0 |
0 |
|
A/mm |
22 |
22 |
30 |
30 |
30 |
30 |
40 |
40 |
40 |
40 |
48 |
48 |
48 |
48 |
53.5 |
53.5 |
|
B/mm |
16 |
16 |
19 |
19 |
19 |
19 |
24 |
24 |
24 |
24 |
27 |
27 |
27 |
27 |
30.5 |
30.5 |
|
Smax/mm |
5 |
10 |
6 |
15 |
23 |
30 |
9 |
19 |
25 |
37 |
12 |
20 |
36 |
46 |
18 |
31 |
|
Ymax/mm |
6 |
11.5 |
10 |
19 |
28 |
36 |
13 |
24 |
36 |
50 |
17 |
31 |
47 |
60 |
24 |
40 |
|
Weight/g |
18.9 |
20.6 |
40.8 |
44.3 |
48 |
52 |
74.4 |
85.5 |
96.5 |
105.5 |
104.3 |
121.2 |
140.8 |
157.8 |
158.1 |
186.6 |
|
Pushing force on fingertip/N |
4 |
3.8 |
8 |
7 |
5.6 |
4.6 |
12 |
11 |
8.5 |
7 |
19 |
17 |
13.5 |
11 |
26 |
25 |
|
Single finger load coeffic- ient/g |
Vertical |
200 |
180 |
370 |
300 |
185 |
150 |
560 |
500 |
375 |
300 |
710 |
670 |
600 |
500 |
750 |
750 |
Coated |
290 |
300 |
480 |
500 |
380 |
300 |
690 |
710 |
580 |
570 |
1200 |
1300 |
1100 |
1000 |
1600 |
1750 |
|
Maximum Operating frequency (cpm) |
<300 |
||||||||||||||||
Standard working lifespan/times |
>3,000,000 |
||||||||||||||||
Working pressure/kPa |
-60~100 |
||||||||||||||||
Air tube diameter/mm |
4 |
6 |
Our Business
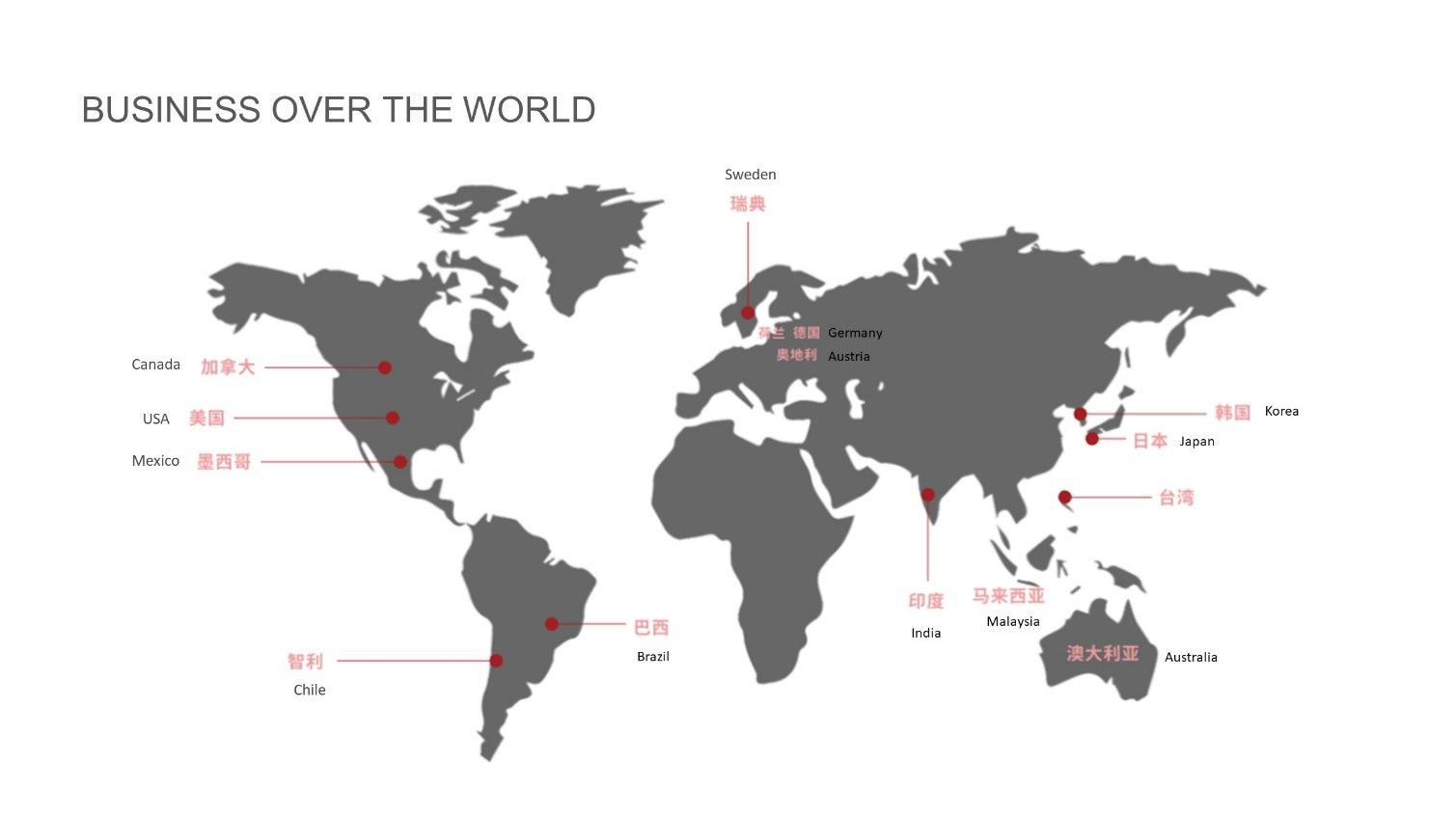
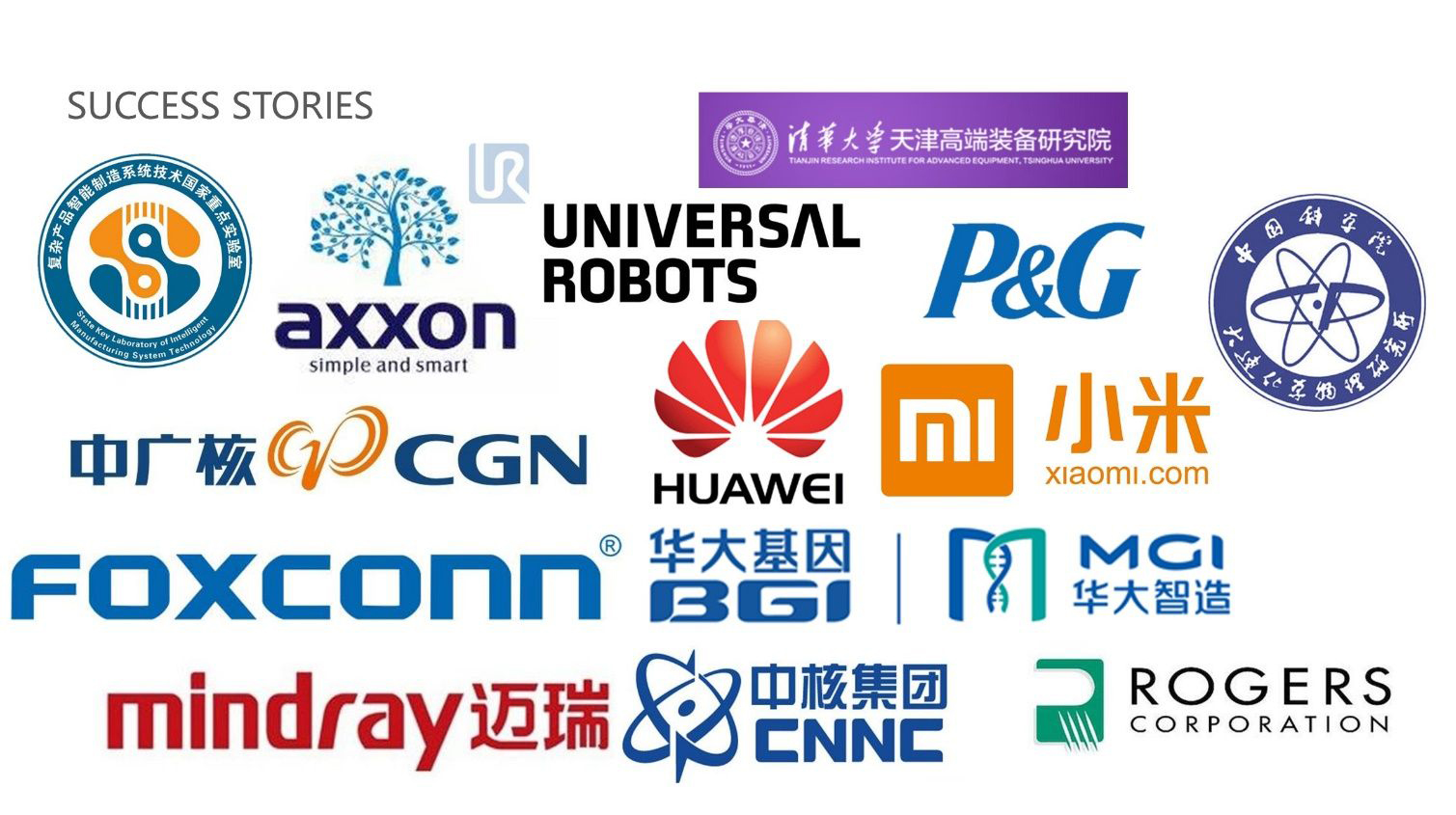